
Best Practice Hygienic Design:
Our engineers have specialised in creating highly effective sealing and guiding systems that comply with the latest best practice in hygienic design, taking into account our customers’ performance and Cost of Ownership requirements.
Careful material selection depends on the expected seal service life taking into account the anticipated operating temperatures, solvents and cleaning / sterilisation agents used during Clean-In-Place (CIP) / Steam-In-Place (SIP) cycles.
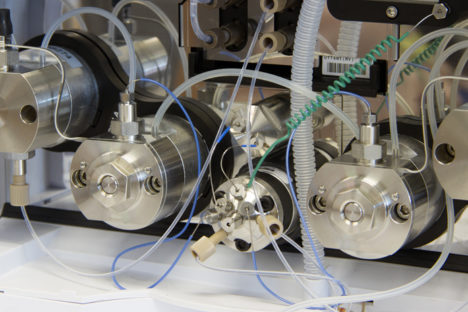
Typical applications include:
• 40 bar actuators & manifolds
• Rotary joints (distributors)
• Filling valves
• Dosing heads
• Pumps & valves
• Capping machines
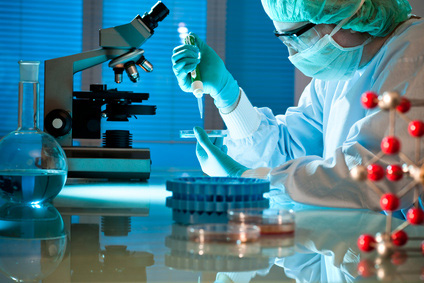
Complete traceability:
Complete material traceability is de rigueur at Repack-S, from the raw ingredients, on all specified USP Class-VI certified, 3-A, FDA, REACH, food contact EC1935/2004 and EC10/2011 compliant thermoplastics and elastomer compounds. Furthermore, all material stocks are thoroughly inspected and process traceability is guaranteed at every stage of seal manufacture.
Seals and bearings are often in direct contact with the product. To prevent cross-contamination, we not only strive to achieve the best possible surface finish but we also meticulously inspect and measure every part, applying sophisticated quality control measures to ensure dimensional accuracy and surfaces that are free of defects and inclusions.
Repack-S sealing solutions include a range of proven seal designs: HPX®-Mono®, DANAFLEX®, DANAROTO®, DANAWING®, DANAGLIDE®, DANACAP® and DANASTEP®. All these solutions, when specified properly, offer highly effective, long-lasting and utterly reliable sealing performance.